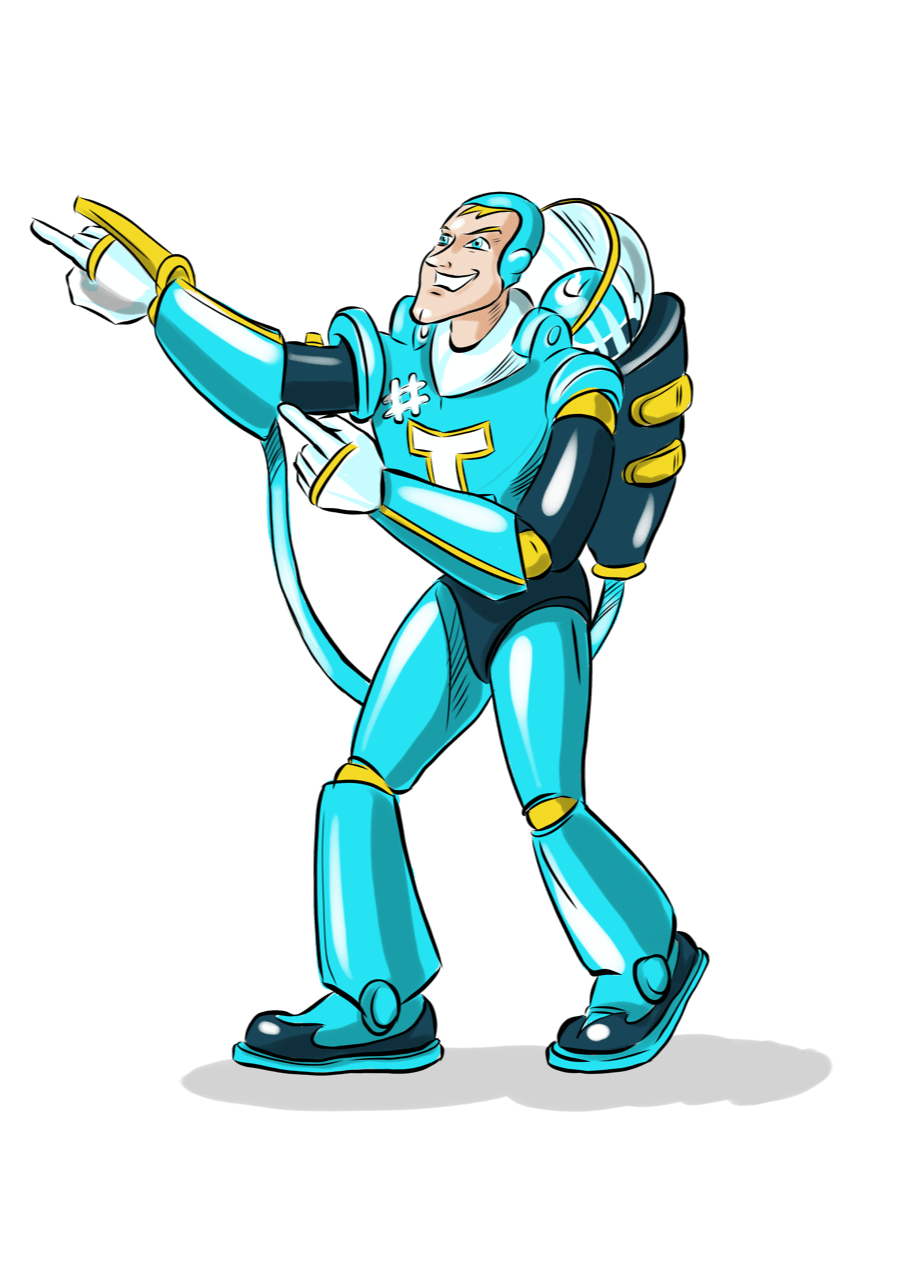
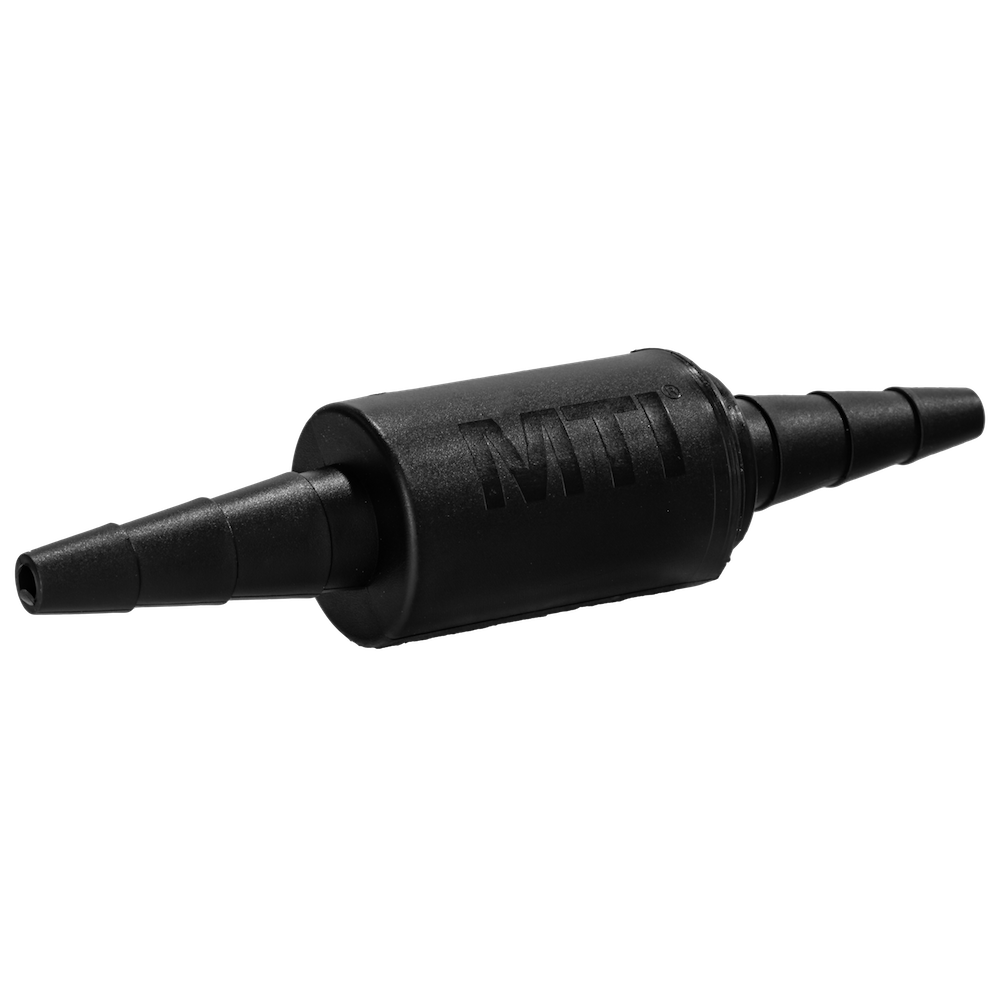
MTI® valve
With the membrane tube infusion process (MTI®) DD-Compound has developed the innovation for vacuum infusion. The uni- que valve® perfects this process.
Challenge
At the beginning of the vacuum infusion a vacuum is placed on the part. During the subsequent infusion the pressure on the part changes compared to the surrounding pressure in line with the quantity of resin infused. By these means, the individual fi- bres of the textile or fabric are raised during the infusion and covered with resin.
The close the under pressure on the part approaches the surrounding pressure, the higher are the fibres raised. This allows them to be covered with even more resin. However, the optimum fibre volume ratio is achieved prior to the highest possible er- ection of the fibres and the associated quantitiy of infused resin.
Answer
The MTI® valve is used in the resin line and controls the resin infusion by means of pressure. During the infusion it represents for the resin infusion a counter-pressure to the under pressure in the part. If this counter-pressure is too big, the valve closes. The resin infusion stops. No more resin enters the part. The valve is adjusted that the counter-pressure becomes too great for the resin at precisely tje point when the necessary under pressure in the part for the fibres to reach an optimum height to be covered in resin is achieved - thut also achieving an optimum fibre volume ratio. Supervising the resin supply is not necessary any more, provided that enough resin exists.
The MTI® valve provides for the steady infusion of the resin in the part. The fibers are evenly covered with resin. It provides for the highest quality of the parts with reproducible results. Besides, it is safe and simply in the use.
The MTI® valve process and the new MTI valve® are suitable for different part sizes and any degree of complexity. They can be used for prototypes, small series and batch production as well as for the mould building.